FAQs
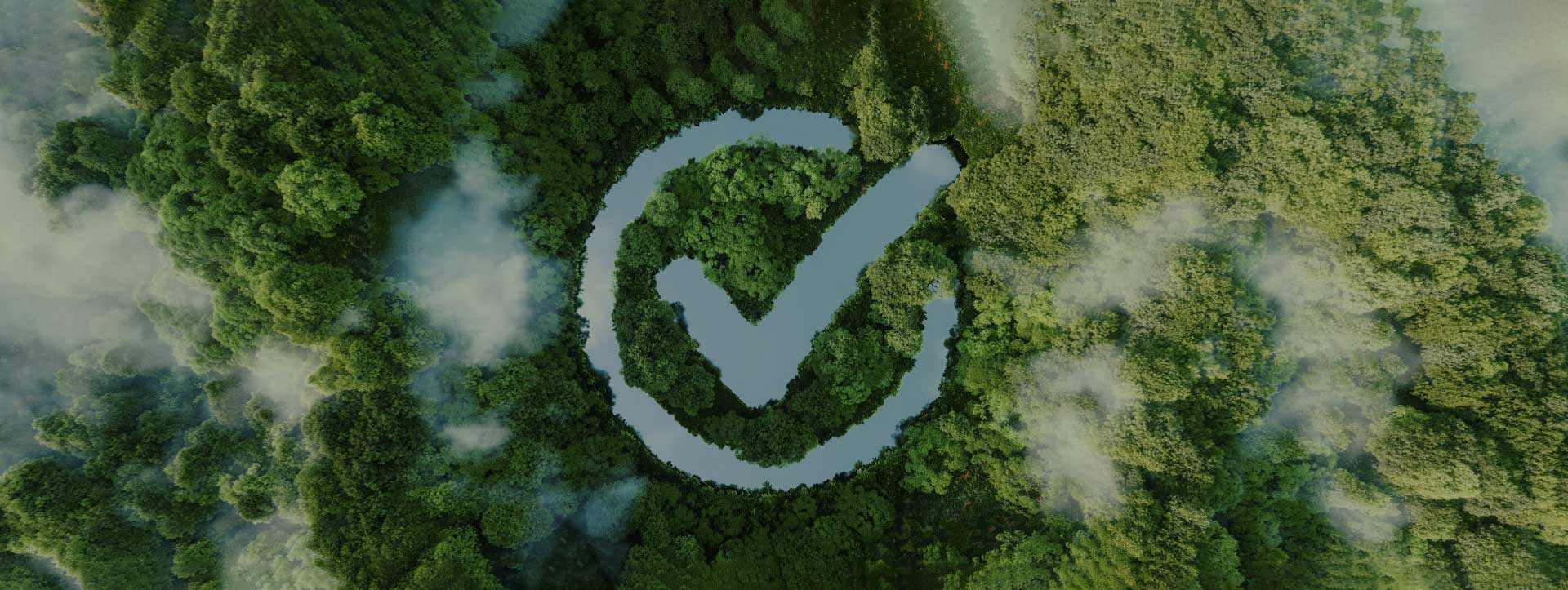
Завод для производства древесного угля
Какое сырье может быть использовано для карбонизации?
1. различные виды биомассы, такие как опилки, рисовая шелуха, скорлупа кокосовых орехов, пальмовая скорлупа, солома, отходы сельского и лесного хозяйства и т. д.
2. городские осадки;
3. бытовые отходы, электронные отходы и т. д.
Целью обработки биомассы является в основном получение биоугля.
Целью обработки осадков и отходов является уменьшение количества осадков и отходов.
Можно ли на одной установке карбонизировать все типы материалов?
Нет. Поскольку время и температура карбонизации, необходимые для биомассы, осадка и различных видов отходов, различны, то и конечные продукты получаются разными. Для разных видов сырья рекомендуется использовать разные печи, чтобы применять разные температуры.
Каковы требования к подаче сырья?
Размер ≤20 мм (лучше 5-8 мм),содержание влаги ≤15%.
Какова производительность пальмового волокна (EFB)?
Плотность пальмового волокна с влажностью 15% составляет около 200 кг/м3. При переработке на оборудовании BST-50 производительность составляет около 2 т/час без гранулирования и около 4 т/час с гранулированием.
Существуют различные виды сырья, все ли они могут быть карбонизированы на оборудовании BESTON?
В первую очередь необходимо подтвердить категорию сырья (относится ли оно к той или иной категории), которое должно просто удовлетворять условиям подачи.
Какие конечные продукты могут быть получены и какова область их применения?
Конечный продукт | Использование |
---|---|
Древесный уголь | Далее перерабатывается в BBQ-уголь или активированный уголь; Используется для изготовления строительного кирпича из глины;. Для улучшения качества почвы. |
Древесный уксус | Используется в качестве инсектицида; Для нейтрализации пестицидов; Для улучшения качества почвы. |
Деготь | Для плавления биодизельного топлива; Широко используется в производстве водонепроницаемых и антикоррозионных материалов. |
Горючий газ | Используется в качестве топлива или для сушки; Используется для производства электроэнергии; Для обогрева тепличных комбинатов. |
Указанные конечные продукты могут быть использованы в следующих областях:
Промышленность
Сельское и лесное хозяйство
Выплавка металлов
Индустрия торговли углеродными кредитами
Можно ли утилизировать горючие газы, образующиеся в процессе карбонизации? Для чего он может быть использован?
При необходимости клиенты могут использовать специальные контейнеры для сбора на объекте. Благодаря высокой теплотворной способности горючего газа он может быть использован для отопления при сжигании, выработки электроэнергии в котлах и т. д.
Если влажность сырья составляет 10%, а 30% конечного продукта – древесный уголь, то какова доля оставшихся 70%?
Около 51% горючего газа, 8% древесного уксуса, 2% дегтя, 7% воды и 2% пыли.
Какое количество горючего газа может быть получено?
Теоретически на каждый 1 кг биомассы образуется 0,7 кг горючего газа.
Сколько углерода может быть произведено?
Выход углерода зависит от температуры и частоты карбонизации сырья. Наше оборудование управляется с помощью частотного преобразования и может быть в любой момент отрегулировано в соответствии с вашими требованиями. Если взять в качестве примера древесную щепу, рисовую шелуху или измельченную кокосовую скорлупу, то из каждой тонны сырья с влажностью менее 10% можно получить 260 кг-310 кг древесного угля, что в принципе позволяет поддерживать соотношение выхода древесного угля 3:1.
Каково время реакции материала?
Как правило, весь процесс карбонизации занимает 15-25 минут.
Что может быть использовано в качестве материала для нагрева? Время предварительного нагрева?
Дизельное топливо, сжиженный газ, природный газ, горючие газы от оборудования для карбонизации. 60-90 мин.
Сколько времени занимает весь процесс карбонизации?
Примерно 15-25 минут.
Какова производительность оборудования для производства древесного угля?
BST-10 Производительность: 2-4 м³/ч (1000 кг/ч);
BST-30 Производительность: 7-9 м³/ч (3000 кг/ч);
BST-50 Производительность: 10-15м³/ч (5000кг/ч);
BST-05 Pro Производительность: 0,3-0,5м³/ч (300кг/ч).
Как увеличить производство древесного угля?
Снизить температуру реакции материала и сократить время реакции карбонизации материала.
Соответствует ли оборудование экологическим нормам выбросов?
Да. Однако в разных странах/регионах требования к выбросам несколько отличаются. Вы можете прислать местные требования к выбросам, и наша техническая группа подберет подходящий процесс обработки выхлопных газов в соответствии с требованиями.
Безопасна ли установка для производства древесного угля?
Безопасность. Этому вопросу мы всегда придавали большое значение. Весь процесс карбонизации происходит в среде с низким содержанием кислорода и отрицательным давлением, материал внутри самого карбонизационного оборудования не контактирует с кислородом и не имеет условий для горения, а в торце оборудования предусмотрены взрывозащищенные устройства, обеспечивающие безопасную эксплуатацию оборудования.
Можете ли вы показать, где производится ваше оборудование?
В основном клиенты неохотно посещают свои производственные площадки, нам необходимо общаться с клиентами. Однако на нашем заводе есть опытная машина, на которой можно увидеть все производственное оборудование, и наша опытная машина также часто помогает клиентам проводить эксперименты по проверке процесса, полностью проверять процесс карбонизации материала и качество готового карбонизированного продукта, чтобы облегчить ваши заботы.
Какова цена на оборудование для производства древесного угля?
Мы специализируемся на оборудовании для карбонизации и можем подобрать различные конфигурации и модели в соответствии с вашими потребностями в производительности, а также цены в соответствии с вашими требованиями. Как правило, стоимость оборудования серии BST начинается от 80 000 до 400 000 долларов.
Какова степень использования и срок службы оборудования для производства древесного угля?
5500 – 5800 часов в год. Срок службы системы карбонизации составляет примерно 5-8 лет. По окончании срока службы требуется замена только системы отвода дымовых газов и трубопроводов, а основной реактор можно продолжать использовать после капитального ремонта.
Пиролизная установка для шин/шлама
Какие материалы могут быть переработаны на пиролизной установке?
Отработанные шины, резина, пластмассы, тканые мешки, акрил, медицинские отходы (инфекционные отходы), нефтесодержащие шламы, гудроновый шлак и другие материалы, содержащие нефть, могут быть пиролизной фазой материала, специальные материалы требуют специального анализа или определения пробы испытания.
Можно ли использовать в пиролизной установке все виды шин?
Нормальный диаметр 1200 мм или меньше может быть непосредственно в более чем 1200 мм должны быть раздавлены. BLJ-3 поставки по умолчанию дверь печи для овальной длинной двери (с дверным валом, размер двери 1100 * 800 мм), рекомендуется, что размер подачи раздавить до 100-200 мм искусственного подачи, BLJ-3, если гидравлический корм, если резиновый блок размер не превышает 600 мм. 6 тонн, 10 тонн, и 16 тонн длинная дверь размером 1800 * 800 мм, с дверным валом. 6 т, 10 т и 16 т длинная дверь печи размером 1800*800мм, с дверным валом.
Можно ли одновременно пиролизировать пластик и шины?
Одновременная обработка пластика и шин не рекомендуется, лучше всего проводить раздельную обработку. Поскольку пластиковый крекинг склонен к засорению системы парафиновым маслом, в соответствии с необходимостью поддержки системы каталитической башни, в то время как шинный крекинг не имеет вышеуказанных проблем; кроме того, шинный крекинг сажи может быть дополнительно обработан и использован, в то время как пластиковый остаток является общим промышленным твердым отходом, смешанный крекинг остатка снизит ценность шинного крекинг сажи, рекомендуется классифицировать и разделять обработку качества и повысить добавленную стоимость продукта.
Каковы требования к подаче сырья?
Прерывистая подача: для ручной подачи, гидравлической подачи, диаметр шин и пластика менее 1,2 м может подаваться напрямую (BLJ-6; BLJ-10; BLJ-16); BLJ-3 требует размера посылок менее 0,6 м.
Спиральная подача: шины ≤ 5 см, пластик ≤ 5 см, влажность 10% или менее, BLJ-3 не имеет решения для спиральной подачи, для конструкции фронтального шлака.
Какова производительность различных материалов в пиролизном установке?
BLJ-3: шины: 1-3 т; пластик 0,5-1 т; шлам 3 т
BLJ-6: Шина: 4-6 т; пластик 2-3 т; осадок 6 т
BLJ-10: Шина: 8-10 т; пластик 3-5 т; шлам 10 т
BLJ-16: Шина: 12-14 т; пластик 6-8 т; шлам 15-20 т
BLL-16: Шина: 8 т;
BLL-30: Шина: 1,04-1,25 т; пластик 0,83-1,04 т; нефтешлам 1,875-2,08 т
Каков выход масла для обработки шин и пластмасс?
Шины в целом: 35-45% масла, 30-35% сажи, 8-15% газа, 8-15% стальной проволоки.
Пластик: смешанный с различными компонентами пластик не имеет определенного значения, необходимо провести испытания на образцах, в целом для очистителя или отдельного пластика содержание масла составляет 40-60% (эти данные основаны на опытных данных), содержание масла зависит от скорости разогрева и некоторых различий в данных лабораторных испытаний между 70-80% содержания масла.
Образуются ли при этом сточные воды, отработанные твердые частицы и нефтяные остатки?
Сточные воды в водяном уплотнении и распылительной башне могут испаряться при высокой температуре в помещении для сжигания отработанных газов и в топочной камере, остаточное масло в баке для мазута может непосредственно вводиться в основную печь для повторного крекинга или смешиваться непосредственно с крекинг-маслом после наслоения, а высокотемпературный выброс дымовых газов после очистки отработанных газов будет соответствовать нормам, и не будет выброса отработанных твердых частиц.
Соответствует ли нормам токсичность отработавших газов?
Стандартная обработка выхлопных газов может только охладить пыль, но у нас есть высокая соответствующая обработка выхлопных газов, которая должна быть выбрана клиентом в соответствии со стандартами выбросов выхлопных газов на месте проекта, самый высокий может соответствовать европейским стандартам выбросов, мы рекомендуем, чтобы клиент в соответствии с их собственными фактическими стандартами выбросов для выбора, нет необходимости во всех высоких соответствующих.
Каковы области применения и каналы сбыта шинного мазута?
Пиролизное масло из шин может использоваться в качестве мазута для прямого сжигания, обычно продается стекольным, металлургическим, электростанциям, керамическим, цементным и другим энергоемким предприятиям, а также продается на нефтеперерабатывающие заводы для глубокой переработки с получением товарного дизельного топлива, а также может быть перегнано для получения компонентов тяжелого масла для генераторных установок для выработки электроэнергии на тяжелом масле.
Можно ли использовать мазут для производства дизельного топлива?
Мазут подвергается дальнейшей перегонке для удаления бензиновой составляющей, а полученная дизельная составляющая может быть подвергнута последующей глубокой переработке и смешиванию для получения товарного дизельного топлива.
Что необходимо знать о дроблении пластмасс?
PVC и PET и другие аналогичные хлорированные и оксигенированные пластики не рекомендуются для обработки; для подачи рекомендуется прессование или экструдирование и гранулирование; согласование крекинга и каталитических башен, специальных катализаторов и систем регенерации катализаторов.
Сколько времени занимает процесс пиролиза?
прерывистый тип: BLJ-6 (шина): подача 2 ч+подогрев 3 ч+пиролиз 7-8 ч+охлаждение 5 ч+разгрузка 2-3 ч, всего 19-21 ч
BLJ-10 (шина): подача 2-3 ч+подогрев 3 ч+пиролиз 8-9 ч+охлаждение 5 ч+разгрузка 2-3 ч, всего 20-23 ч
BLJ-16 (шина): подача 3 ч + подогрев 3 ч + пиролиз 10-11 ч + охлаждение 6 ч + выгрузка 3 ч, всего 25-26 ч. Время обработки пластика и шлама может быть увеличено на 3-4 ч по отношению к времени обработки шины. + охлаждение 6 ч + выгрузка 3 ч, итого 25-26 ч
Пластмассовое и шламовое сырье может быть отнесено к времени переработки шин для увеличения времени пиролиза соответственно на 3-4 ч.
Полуавтоматический: BLL-16 (гранулы из шин): подача 2 ч + предварительный нагрев 3 ч + пиролиз 8 ч + охлаждение 3 ч + выгрузка 3 ч, всего 19 ч 56 ч для обеспечения производительности переработки 3 партий
Какие виды топлива могут быть использованы и каков их расход?
Можно использовать природный газ, дизельное топливо и тяжелые нефтепродукты. Расход конкретно зависит от модели. Горелки на природном газе стоят дороже, горелки на тяжелом масле и дизельном топливе – до 400 000 калорий, разовый расход топлива – 40-50 л/ч.
Как очищать сточные воды, образующиеся при пиролизе?
1. В основную печь для повторной реакции;
2. Подключение водяной трубы к выхлопной камере горения плюс сопловое горение
3. Централизованный сбор и передача на очистку в систему внешней канализации.
Каков расход воды на производство и эксплуатацию оборудования?
16 тонн, расход воды 0,5-1 тонна/сутки, BLL-30 полный непрерывный водооборот, в основном испарение охлаждающей воды 3 тонны/сутки.
Каков примерный срок службы, гарантия и стоимость монтажа пиролизного оборудования?
5-8 лет, в течение которых достаточно заменить основную печь и несколько быстроизнашивающихся деталей; один год, но мы предлагаем пожизненное техническое обслуживание и бесплатное обновление программного обеспечения; онлайн-установка 50$/день, офлайн-установка 100$/день, при этом клиент также обязан оплатить авиаперелет и страховку наших инженеров после продажи, визовые расходы, расходы на профилактику эпидемий, питание, проживание, транспорт, местные медицинские расходы и другие расходы, понесенные на территории клиента.
Какие защитные устройства имеются на данном оборудовании?
Аварийный эвакуационный клапан, устройство защиты от обратного удара жидкости с трещиной, пламегаситель, сигнализатор перегрева и избыточного давления, технология каталитического растрескивания пластика, поддерживающая высокотемпературное уплотнение гибкой мягкой набивкой.
Каков срок изготовления и монтажа оборудования?
Стандартный срок производства составляет 30 рабочих дней для установки на салазках, установки периодического и полунепрерывного типа 100 рабочих дней для установки непрерывного типа.Стандартный срок монтажа составляет 45 рабочих дней для пирализных установок периодического и полунепрерывного действия, 60 рабочих дней для пирализных установок непрерывного действия и 15 рабочих дней для BLJ-3.
Возможно ли использование электрической системы отопления?
Во-первых, мы не предоставляем систему электрического отопления; во-вторых, по нашему мнению, стоимость системы электрического отопления очень высока; в-третьих, потребление энергии в час очень велико, например, оборудование BLJ-16 потребляет около 1 000 кВт в час. Кроме того, наша команда R&D работает над экспериментальной моделью отопления горячим воздухом, которая может улучшить равномерность нагрева и снизить потребление энергии при эксплуатации.
Сколько рабочих необходимо для эксплуатации оборудования?
На периодическом пиролизе обычно работают 3-5 человек в одну смену. Полная непрерывная система комплектации представляет собой трехсменную ротационную работу, в каждой смене которой работает не менее 6 человек, в том числе 1 человек на посту централизованного управления, 2 человека на посту шлакоудаления, 2 человека на посту подачи и 1 человек на посту контроля. В то же время для устранения механических неисправностей, возникающих в процессе непрерывного производства и эксплуатации, необходимо выделить 1 сварщика и 1 электрика, которые будут централизованно устранять неисправности оборудования в дневную смену, таким образом, общая численность персонала составит 18-20 человек.
Станок для производства яичных лотков
Какие виды сырья могут быть использованы?
Картонные коробки, оберточная бумага, книги, тетради, бумага формата A4, бумага для документов, целлюлоза и т. д.
Каково соотношение воды и бумаги?
Соотношение эталонных масс 6:1-5:1 в соответствии с нашей конфигурацией гидроразбивателя высокой консистенции.
Какова масса влажных и сухих яичных лотков?
Единичная масса изделий из мокрого яичного лотка составляет 200-350 г; единичная масса изделий из сухого яичного лотка обычно 80-100 г; детали могут быть скорректированы в соответствии с требованиями заказчика, с добавлением вспомогательных веществ. Весовой коэффициент лотка для мокрых яиц -Токарный станок 80*3,5 -4-сторонний станок 80*3 -8-сторонний станок 80*2,5.
Что можно сделать с конечным продуктом?
Яичные лотки, картонные коробки для яиц, лотки для кофейных чашек, лотки для обуви, промышленная упаковка, лотки для фруктов, лотки для вина, лотки для рассады.
Какова высота яичных лотков?
В норме – не более 5 см, в патологии – не более 8 см.
Что такое сушка?
Сушка заключается в использовании топлива для создания горячего воздуха, который поступает в сушильную камеру и обеспечивает температуру в ней около 200 градусов. Горячий воздух циркулирует и уносит влагу из влажного лотка, в результате чего получается сухой готовый лоток.
В чем преимущества металлической сушильной линии?
Экономия расхода топлива по сравнению с кирпичом; Не требует подготовки материалов, монтажа, прост и удобен в установке; Малая занимаемая площадь; Металлосушка 6-слойная.
Сколько времени необходимо для сушки?
Около 17-18 минут на металлической сушильной линии.
Какова температура в сушильной камере?
Металлосушка: 200-210 градусов сверху, 150 градусов в центре и 80-90 градусов снизу.
Какие условия работы подходят?
Ограниченные площади и высокие трудозатраты
Можно ли на одной форме разместить картонные коробки для яиц, яичные лотки?
Нет. Поскольку вакуумное положение пресс-формы фиксировано, форма и размер пресс-формы напрямую влияют на вакуумную эффективность всей конструкции. Кроме того, из-за различий в высоте, площади, количестве отверстий и расположении пресс-форм может возникнуть ситуация, при которой степень вакуума будет нестабильной, а эффект формовки не будет хорошим. Рекомендуется использовать один и тот же тип форм для одного макета, например, все лотки для яиц, все коробки для яиц, все фигурные формы.
Каков срок службы алюминиевых и пластмассовых пресс-форм?
2-3 года для пластмассовых форм, 5-8 лет для металлических форм.
В чем разница между алюминиевыми и пластмассовыми пресс-формами?
Алюминиевые пресс-формы имеют длительный срок службы, пластмассовые – экономически выгодны.
Каковы размеры пресс-форм для пластмасс?
Размер пресс-формы: 290*290 мм, 295*295 мм, 300*300 мм.
Каков срок изготовления и стоимость алюминиевых пресс-форм?
Срок изготовления алюминиевых пресс-форм, не требующих вскрытия, составляет 45 дней, а цена относится к цене различных алюминиевых пресс-форм; для новых алюминиевых пресс-форм, которые вскрываются, срок изготовления составляет 65 дней, и помимо цены самой пресс-формы необходимо увеличить соответствующую плату за вскрытие.
Требуются ли присадки? Какова концентрация добавки?
Как правило, добавки не требуются. Достаточно смешать воду и бумагу. Если нужен цвет, можно добавить красящие добавки. Если необходимо повысить степень адгезии, возьмем в качестве примера тальк. Если необходимо добавить тальк для достижения высокой степени фиксации, следует использовать систему обработки наполнителя. Водную суспензию, содержащую от 20% до 30% талькового наполнителя, обработать в смесителе на высокой скорости в течение 6 минут, разбавить водой и добавить химические добавки, обработать в течение 5 минут для приготовления суспензии наполнителя и затем добавить в суспензию.
Каково время работы взбивателя?
Обычно около 20 минут, время регулируется в зависимости от сырья
– Мягкая бумага: газета, бумага формата А4 15-20 минут
– Твердая бумага: гофрокартон 30-40 минут
– Высокопрочная бумага: бумажный джем 50 минут
Необходимо ли добавлять вспомогательное оборудование для оптимизации производственного процесса?
Собирающая машина – одинаковое количество яичных лотков в каждой упаковке; Упаковочная машина – экономия места; Термопресс – улучшает внешний вид продукта, делает его более гладким; Виброгрохот – удаление примесей; Рафинировочная машина – делает мякоть более нежной.
Какое количество примесей может отделить вибрационный грохот?
Примеси диаметром более 4 мм.
Есть ли шум?
Основным источником шума в оборудовании является вакуумный насос. Для решения проблемы шума на вакуумном насосе могут быть приняты соответствующие меры по звукоизоляции. У нас есть готовые решения.
Beston Service
Каковы основные виды деятельности компании?
Beston занимается производством оборудования для переработки отходов пластика/шин/резины/нефтяного шлама, переработки биомассы, утилизации осадков сточных вод, переработки макулатуры, а также решений в области упаковочных технологий и утилизации медицинских отходов, монтажных и пусконаладочных работ, услуг по эксплуатации проектов и т.д.
В чем сильная сторона вашей компании?
По показателям экспортных продаж Китай занимает первое место в отрасли переработки твердых бытовых отходов.
В чем заключаются технические преимущества?
Более 20 старших инженеров с 10-летним опытом работы в отрасли выполняют производственные исследования и разработки, формулируют корпоративные стандарты на продукцию, участвуют в разработке национальных стандартов на аналогичные продукции.
Как предоставлять индивидуальные услуги?
Beston располагает отличными двуязычными инженерами для технической поддержки, а также предоставляет комплексные услуги по настройке оборудования (настройка планировки площадки, настройка конфигурации оборудования и т.д.), чтобы обеспечить потребности клиентов в конфигурации производства и программе оборудования.
Какие сертификаты имеет Beston?
Beston имеет соответствующие технические сертификаты, все они соответствуют сертификации ISO90001.
Как обеспечить качество оборудования?
Заводская проверка оборудования, проверка сырья на складе, производственные испытания, испытания на газонепроницаемость и безопасность, испытания на поставку и монтаж всего процесса по строгим стандартам процедур контроля качества, испытания сторонними профессиональными организациями, полностью гарантируют жизненный цикл оборудования, так что заказчик при эксплуатации оборудования безопасно и бесперебойно получает экономическую выгоду.
Каков срок службы оборудования?
Передовые технологии обеспечивают длительную стабильную работу оборудования на производстве, срок службы составляет до 5-8 лет, что может принести долгосрочную экономическую выгоду клиентам.
Каковы преимущества технологии производства оборудования?
1. Преимущество производства оборудования: более 80% сотрудников имеют более чем 10-летний опыт работы в отрасли, все сотрудники должны пройти предпродажную подготовку в течение 7 дней, что обеспечивает клиентам отличные гарантии качества оборудования.
2. Гарантия качества: оборудование должно быть проверено тремя отделами, включая производственный отдел, отдел контроля качества и проектный отдел, перед тем как выйти с завода, чтобы гарантировать качество продукции.
3. Преимущества производственной техники: Все оборудование изготовлено из стали национального стандарта сварки, строгий контроль спецификации стали; обрабатывающие компоненты все используются в количестве контрольных материалов; совершенная производственная часть из сырья материала, сварки рамы, обработки с ЧПУ, сборки оборудования, тонкой шлифовки и покраски, проверки качества и тестирования всего совершенного производственного процесса.
4. Преимущество непрерывной работы оборудования: Стабильность работы оборудования зависит от баланса центральной точки процесса сварки стойки; точности процесса сборки оборудования; вспомогательных аксессуаров – все они используют бренды первой линии: такие как Delisi, Baxter, Siemens, Schneider и т.д.